Breathing a new lease of life into your Lindström Precision Cutters
The Lindström Reconditioning Service goes beyond routine maintenance. As Precision Cutter specialists, we know how important it is to work with exceptionally sharp tools that deliver accurate cuts day after day. As such, we maximize the lifespan of your Lindström Precision Cutters, delivering exceptional performance while minimizing the impact on the environment, and your wallet.
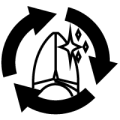
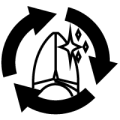
A meticulous inspection
We inspect, recondition and test each Precision Cutter in our lab to deliver tools that excel in accuracy and performance
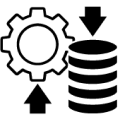
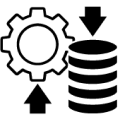
Cost-effective solution
By maximizing the life of your existing tools, we help reduce overall costs and optimize your budget
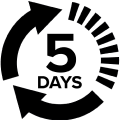
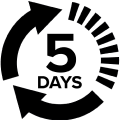
Committed to efficiency
A turnaround of just 5 days ensures your operations remain on schedule
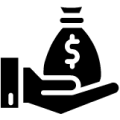
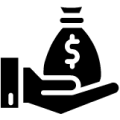
Resourceful spending
Our Precision Cutters are more economical than lower-quality cutters in the medium or long term, thanks to the increased number of precise cuts.
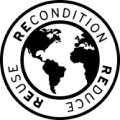
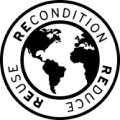
Recondition, reduce, reuse
Extend the lifecycle of your most critical tools, reducing your environmental impact and contributing to the circular economy.
SWIFT TURNAROUND
Lindström’s commitment to efficiency and optimal workflow ensure your precision cutters’ reconditioning does not suffer unnecessary delays. We prioritize a swift turnaround of five days to minimize downtime and keep your operations running smoothly.
Express Service: For urgent reconditioning needs, ensuring minimal disruption to your business and production schedule.
Responsive Customer Support: From initial inquiries to scheduling and post-service support, our team prioritizes clear and prompt communication.
COST OF OWNERSHIP
Spend resourcefully. Recondition and refurbish your Lindström Precision Cutters at half the retail price and at a much lower environmental cost.
The best way to compare the real cost of precision cutters is to consider the number of cuts per tool.
Lindström tools (representing a higher initial investment) are more economical in the medium or long term than lower-quality cutters.
WHAT DOES OUR RECONDITIONING SERVICE INCLUDE?
- A thorough inspection to identify wear and damage, replacing the spring and/or joint screw if necessary
- Sharpening and chamfering each blade as needed, and checking the jaws are parallel when closed
- Surface lubrication to ensure smooth and consistent movements, and new ESD safe handles for optimal ergonomics
- Rigorous quality assurance checks to ensure your Precision Cutters meet our stringent criteria
- This service is exclusively reserved for Lindström Precision Cutters (see below for a complete list of eligible models)
- Lindström Precision Cutters will only be reconditioned once
- For reconditioning or exchange requests a minimum order quantity of 20 units is required
* Certain damages will not be reconditioned through the service, such as: broken tips, broken metal handles, broken joints or excessive divots in the cutting blades. Look at the following link to see examples.
ARE MY PRECISION CUTTERS ELIGIBLE
FOR THE RECONDITIONING SERVICE?
View the table below for all eligible Lindström Precision Cutter models.
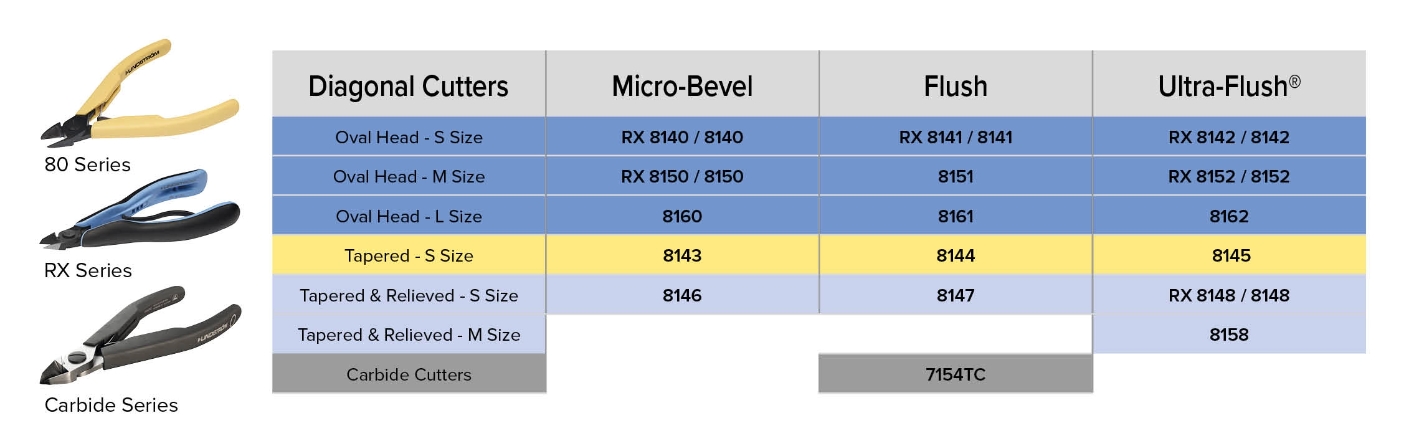
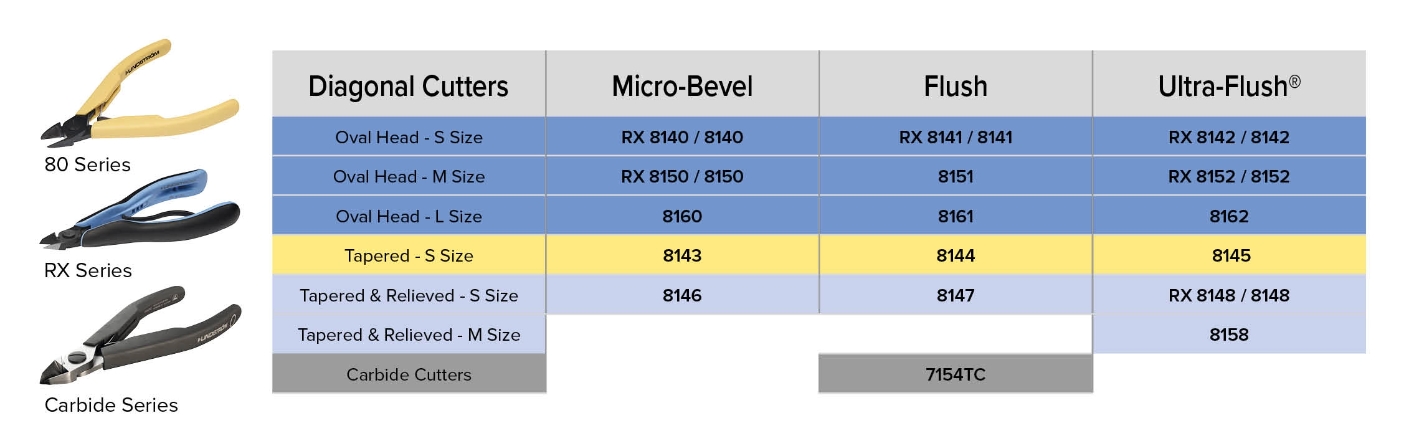


GET IN TOUCH
Contact our Lindström Reconditioning Specialists to discuss your requirements.
Email: [email protected]
Snap-on Industrial Distribution Center
Attn: Lindström Warranty Department
6969 Jamesson Road
Midland, GA 31820